Steel Industry |
Case Study: Management of forged products through
heat treatments using HEATPROOF tags
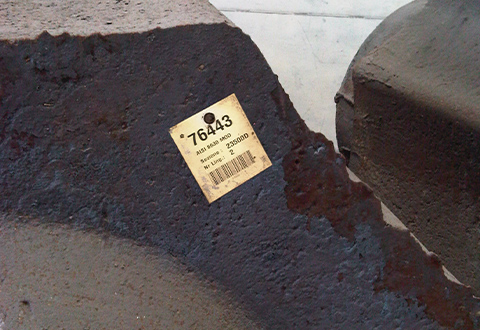
Object | Steel Forged product |
Steel industry | Attach tag at temperatures from room temperature to 800℃ →Heat treatment ( 1100℃ x 18hours ) |
Case5 | HEATPROOF HP-L90 |
Customer’s request
- Improve product tracking
- Eliminate misidentification of products
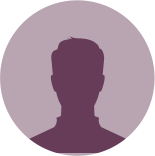
Initial Process Management
Marking by hand with heat resistant chalk
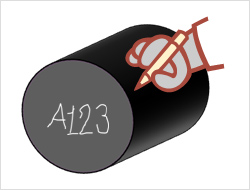
Hand writing on forged products using heat resistant chalk
Hand marking with heat resistant chalk
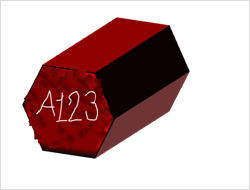
Forged product is produced but may require additional forging processes
Hand marking with heat resistant chalk
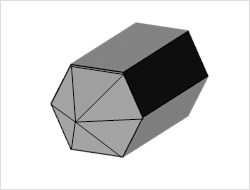
Marking can be lost on final product after cutting work
Process Issues
- Marking is necessary after each heat treatment
- Product is incorrectly identified or hand writing is difficult to read. This leads to identification errors.
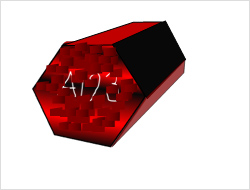
Heat treatment cycles may cause the hand
written mark to be illegible.
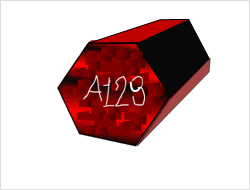
Product misidentification can easily occur
HEATPROOF Solution
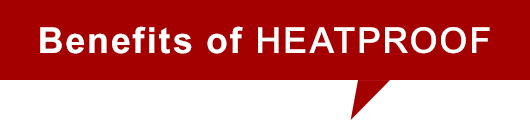
1 | Provide product identification which will survive all processes. |
2 | Eliminate identification errors |
3 | Utilize barcode scanners to verify product identification and eliminate human reading errors. |
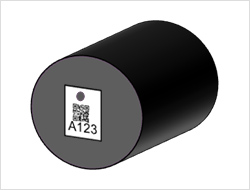
HP-L90 tags can be stud welded, spot welded, or nailed to steel products for heat treatments or repeated forging
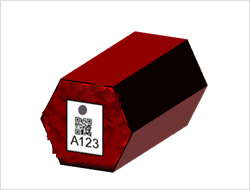
Completion of half-Finish products
HP-L90 tag survives multiple reheat cycles avoiding the need to re-identify products
→ Remarking is not necessary.
→Accurate product tracking through
complete process by using HP-L90 tag with scanable barcodes
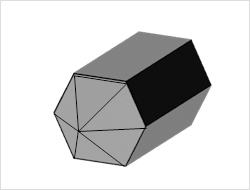
Final product after cutting work
→HP Tag is detached at final process.