Asset Management |
Case Study: Management of injection casting mold
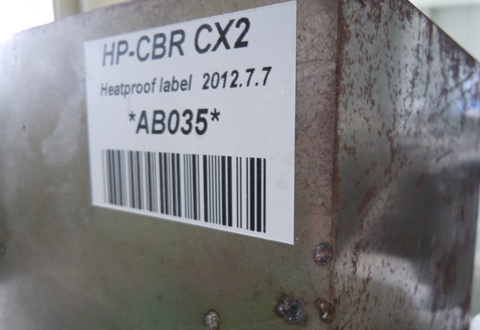
Object | Injection Casting Mold |
Temperature | 200~400℃ x several hours x multiple cycles |
Products | HP-120S HP-150N HP-350N |
Customer’s request
- Eliminate problems caused by poorly identified casting molds
- Use barcode identification which will survive multiple heat cycles
- Scan to verify mold identification at each process
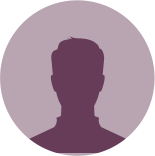
Initial Process Management
Visual inspection of stamp marking to confirm identification
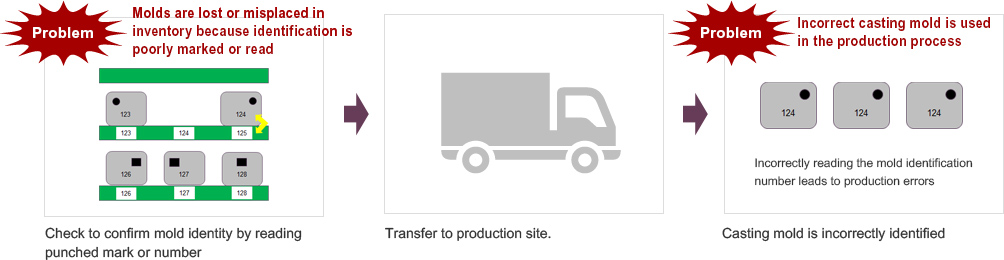
Process Issues
- Mold identification errors occur because of poor marking methods
- Mold identification degrades after multiple processes leading to identification errors
- Production issues occur because of misidentified molds
HEATPROOF Solution
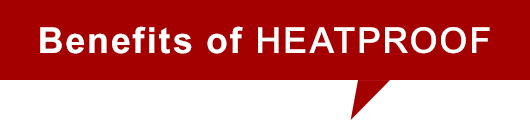
1 | Provide heat resistant identification which can survive multiple cycles |
2 | Introduce a barcoding system which will allow molds to be verified by scanners |
3 | Provide mold identification which will survive outdoor exposure. |
4 | Eliminate the misidentification of molds caused by human error |
5 | Improve the mold tracking system through the production process |
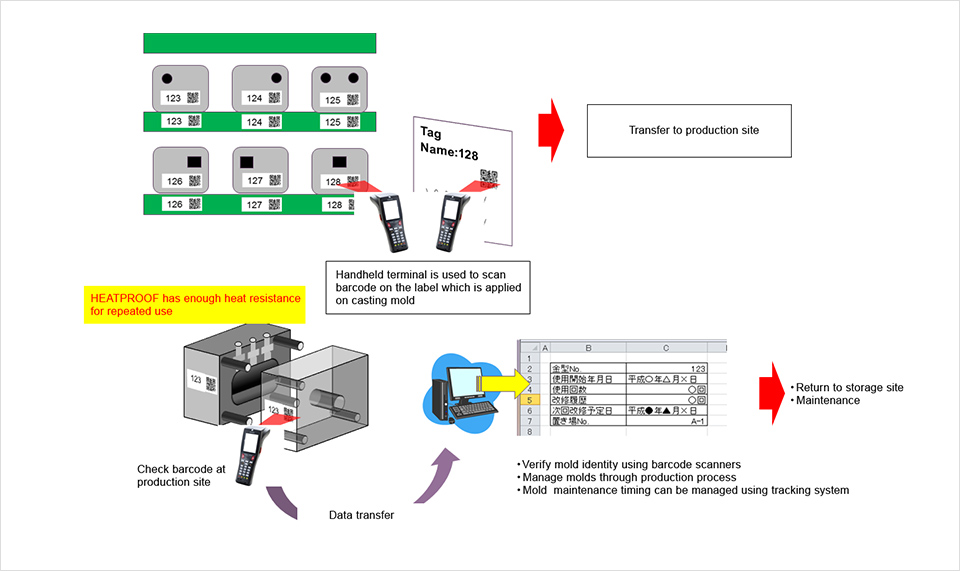